AUBURN — Currier Plastics, Inc., a custom blow-molding and injection-molding manufacturer, is “90 percent complete” with an expansion project that started back in October.
That’s according to John Currier, company president, who spoke with The Central New York Business Journal on April 8.
“We are in the new manufacturing facility right now,” Currier says, noting a warehouse addition is also finished.
(Sponsored)
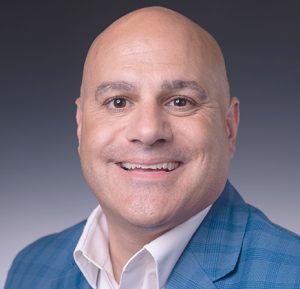
How CH Insurance’s BOOST Program Optimizes Group Benefits for Small Businesses
For small business owners, navigating the complexities of group benefits can be overwhelming. Between compliance regulations, cost considerations, and employee expectations, offering a competitive benefits package often feels like a
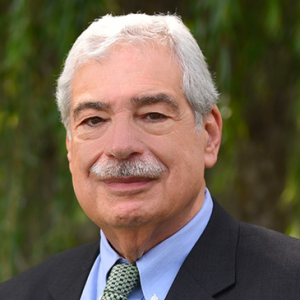
Criminal Liability for Employment Law Violations?
New York employers are often surprised to learn that wage law violations can lead to criminal penalties in addition to financial penalties. Whether payroll is outsourced, or a staffing agency
Meanwhile, the expansion of the office area is about “50 percent” finished, he adds, noting he was speaking during the phone interview from temporary office space, which he’ll vacate in a few weeks.
The project increases the firm’s location from the previous 65,000 square feet to about 120,000 square feet.
Currier Plastics has added equipment annually for the past five years. So, the company “…just basically ran out of square footage,” Currier says.
The manufacturer currently employs 100 full-time workers, and, with the expansion, hopes to add 50 additional full-time workers over the next three years, according to Currier.
Work on the $21 million project began last fall.
The total cost includes $8 million for improvements to the building and infrastructure and $13 million for new equipment purchases in the next three years.
Syracuse–based VIP Architectural Associates, PLLC and VIP Structures, Inc. designed and are handling the expansion project.
Currier Plastics used “mostly” private financing, along with a loan from First Niagara Bank, Currier says. He couldn’t recall the exact amount of the bank loan the company used for the project.
New York state also approved $1 million in Excelsior tax credits, and a $750,000 Economic Transformation from Empire State Development, the state’s primary economic-development agency, to help pay for the project, he adds.
The company is able to apply the tax credits when it buys new equipment.
“They’re helpful,” he says. “[They] certainly weighed heavy in our consideration to stay here [in Auburn].”
The company had considered moving to sites in Pennsylvania and Virginia before deciding to stay in Central New York.
Company growth
When asked why the company pursued the expansion project, Currier simply says, “Business has been good.”
Currier Plastics generated revenue of $25 million in 2012, representing a 12 percent increase over 2011. The manufacturer is projecting a revenue increase of 10 percent in 2013.
Currier Plastics had several years of double-digit sales growth and outgrew its space.
“We had several existing customers and new customers that wanted us to do more work for them, so we either had to turn those new jobs down or expand the facility,” Currier says.
For example, Currier Plastics has generated revenue growth in the molding of packaging containers.
“The packaging area is where we’re most heavily focused,” he says.
The company blow molds bottles and canisters, and injection molds caps and lids for packages, items the industry refers to as “closures,” Currier says.
Currier Plastics, founded in 1982, is also seeing growth in the amenities market, producing packaging for shampoo and mouthwash containers, he says.
John Currier is one of four men who share ownership of the company. The other three owners include John’s brother, James Currier; Gary Kieffer, vice president of new product development; and Michael Cartner, the firm’s CFO.
John Currier declined to disclose the percentage of ownership between the four men but said the percentages weren’t equal.
The company primarily serves commercial clients in the Northeast, especially original-equipment manufacturers (OEM).
“We are a custom manufacturer, so we don’t have any product line … of our own. Everything we make is specifically for an individual customer,” Currier says.
Consulting on CCC program
Currier Plastics is working with Cayuga Community College (CCC) to create its first plastics-technology program, the firm announced April 3.
CCC is using grant funding it obtained last fall to develop an advanced-manufacturing project in the plastics industry for New York and to support work-force development initiatives statewide, according to a news release from Currier Plastics.
“We’ve been assisting them with our expertise in facility layout. We’ve got several individuals that have plastics technology and-or plastics-engineering degrees from Penn State, so we’ve been advising them on the curriculum,” Currier says.
Sam Ware, automation engineer at Currier Plastics, recently spent time with CCC architecture students working on the designs for the new plastics lab, the company said.
The idea is to have an injection-molding machine (IMM) with a press-mounted industrial robot, Ware said in the news release.
“The IMM would have a conveyor tied in so that students could troubleshoot the interfaces between the conveyor system and the IMM. There are also plans for a multi-axis robot that would be on a mobile station so that students could perform different ‘real world’ tasks with it,” Ware said.
CCC plans to eventually build a “mini factory,” which would give students the hands-on learning experience of a real-molding facility.
Cayuga Community College is one of 64 accredited institutions that make up the State University of New York.
Contact Reinhardt at ereinhardt@cnybj.com