In business since 1964, Custom Electronics has spent the past 20 years focusing on the development of new technology in areas such as lithium-ion batteries and energy-storage systems, says Michael Pentaris, company president. He was excited to partner with UB on this new technology that improves the anode part of a battery. Together with a […]
Get Instant Access to This Article
Become a Central New York Business Journal subscriber and get immediate access to all of our subscriber-only content and much more.
- Critical Central New York business news and analysis updated daily.
- Immediate access to all subscriber-only content on our website.
- Get a year's worth of the Print Edition of The Central New York Business Journal.
- Special Feature Publications such as the Book of Lists and Revitalize Greater Binghamton, Mohawk Valley, and Syracuse Magazines
[bypass-paywall-buynow-link link_text="Click here to purchase a paywall bypass link for this article"].
In business since 1964, Custom Electronics has spent the past 20 years focusing on the development of new technology in areas such as lithium-ion batteries and energy-storage systems, says Michael Pentaris, company president. He was excited to partner with UB on this new technology that improves the anode part of a battery. Together with a cathode, the anode forms the part of the battery where energy is stored.
“We’re excited to see that packaged and refined into a complete cell,” Pentaris says of the new anode.
The anode is made of hybrid composite materials rather than the traditional natural and synthetic graphite that forms current anodes, says Christopher Janson senior business-development manager at the Center of Excellence in Materials Informatics. The current process is environmentally challenging, he adds. The new process uses fewer solvents that are aqueous based.
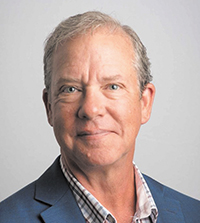
“This new hybrid composite material can be synthesized,” in a more environmentally friendly manner, he says. Along with being better for the environment, it also has an ultra-high capacity.
Batteries with more energy storage are a win for the environment, Janson says. Higher-capacity batteries make electric vehicles a more viable option, for example.
The Center of Excellence in Materials Informatics has been developing the new material for three years now and is ready to test out the next stage — scaling the project for eventual manufacture, he says. That’s where Custom Electronics comes into play.
“We’ll take that and put it into a cell,” Pentaris says. Custom Electronics will look at efficiencies, packaging issues, and troubleshoot any problems like bulging or overheating.
Typically, the University at Buffalo licenses out the technically to a business to take those next steps. Janson is hopeful UB will be ready to license the new technology by late 2023 to hit the market as early as 2024. The ultimate goal is for a New York company — whether it’s Custom Electronics or another — to manufacture the anode and help grow the state’s green economy, he adds.
“We think we’ve got something quite compelling,” Janson says.
Headquartered at 87 Browne St. in Oneonta, Custom Electronics designs, manufactures, and supports capacitors and electronic assemblies for the commercial, medical, and defense markets.
The Center of Excellence in Materials Informatics at UB says it works with manufacturing companies and startups to accelerate research and development, invent new materials, and develop new products.
The Jeff Lawrence Innovation Fund, launched in December 2016, provides more than $1 million in direct assistance annually to the manufacturing, research and development, technology, and entrepreneurial ecosystems. The fund has awarded $7.3 million in funding to support collaborative projects around the state.
FuzeHub is a nonprofit organization that connects small and mid-sized manufacturing businesses to resources, programs, and expertise for technology commercialization, innovation, and business growth.