The average New Yorker probably doesn’t spend a lot of time thinking about recycling or about concrete — or about how those two things could possibly go together. However, a group of dedicated researchers and entrepreneurs in the Southern Tier have been thinking about all of those things — and doing something about it. Their […]
Get Instant Access to This Article
Become a Central New York Business Journal subscriber and get immediate access to all of our subscriber-only content and much more.
- Critical Central New York business news and analysis updated daily.
- Immediate access to all subscriber-only content on our website.
- Get a year's worth of the Print Edition of The Central New York Business Journal.
- Special Feature Publications such as the Book of Lists and Revitalize Greater Binghamton, Mohawk Valley, and Syracuse Magazines
[bypass-paywall-buynow-link link_text="Click here to purchase a paywall bypass link for this article"].
The average New Yorker probably doesn’t spend a lot of time thinking about recycling or about concrete — or about how those two things could possibly go together.
However, a group of dedicated researchers and entrepreneurs in the Southern Tier have been thinking about all of those things — and doing something about it.
Their results are already having an impact on both the recycling world and the construction industry around the region, helping to mark the Southern Tier as a hot spot for green concrete.
The Alfred University Center for Advanced Ceramic Technology (CACT) is working with SQ4D, a Patchogue–based company that 3D prints concrete houses. Together, they are developing a glass aggregate that’s a more environmentally friendly alternative to traditional concrete ingredients.
While the words are commonly used interchangeably, cement is actually just one of the ingredients in concrete. The other ingredients are water and some type of aggregate, says Collin Wilkinson, an assistant professor of glass science and engineering at Alfred. Often made of sand and/or crushed stone, the aggregate really is there to take up space and create more concrete volume, he says.
The problem is that mining for and then crushing and drying that aggregate isn’t always the most environmentally friendly process. That’s why CACT began working with SQ4D to find an alternative. As home to the Center for Glass Innovation, it’s no surprise researchers began looking to glass as an option, Wilkinson says.
Glass was a good choice — replacing about 20 percent of traditional aggregate — because it is made primarily of the same elements as limestone with a few added ingredients that don’t work quite as well.
“How are we going to modify this waste glass?” Wilkinson asks. That was the question they sought to answer.
The other reason to use waste glass? There’s a lot of it, he says.
The founders of KLAW Industries in Binghamton discovered that when they toured a recycling facility while still in college.
“We learned a lot of glass we recycle doesn’t actually get recycled,” COO Jacob Kumpon says. “Glass is very difficult to process.”
He and KLAW co-founders Jack Lamuraglia and Tanner Wallis, wanted to find a solution for that.
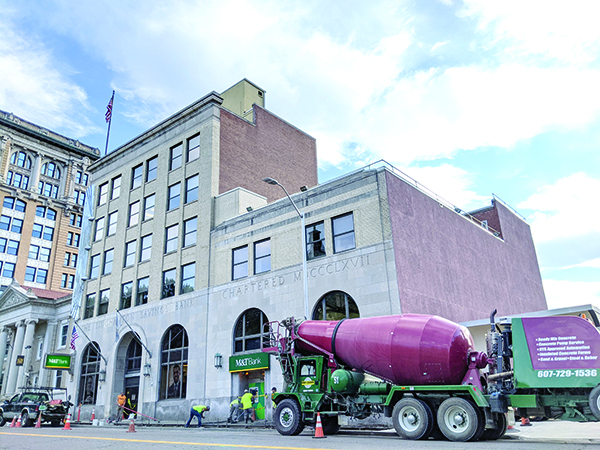
Their solution, Pantheon, uses waste glass that’s ground to about the same consistency as baby powder in place of a portion of the cement used to make concrete. Pantheon costs about the same as cement and uses the same tools and equipment, but the resulting concrete is proving to be about 11 percent stronger. Its creation also creates 97 percent less emissions than traditional cement production.
The City of Binghamton recently partnered with KLAW for $1.7 million worth of curb and sidewalk upgrades throughout the city. Barney & Dickenson Inc. of Vestal delivered the low-carbon concrete for the project and is a regular KLAW customer.
Earlier this year, the U.S. Department of Energy awarded KLAW and the Koffman Southern Tier Incubator $125,000 for its Energy Program for Innovation Clusters (EPIC) Prize Pitch Competition to expand low-carbon concrete throughout the state — funding that will help KLAW scale up its production of Pantheon.
Heading into 2024, Kumpon estimates KLAW will be able to create about 320 tons of Pantheon each month, while diverting 400 tons of waste glass away from municipal recycling facilities every month.
These new glass-based materials come at a time when there is a big push to decarbonize the construction industry. In New York state, a new “Buy Clean Concrete” mandate goes into effect in 2025, that will require environmental product declarations (EPD) for all concrete mixes used in qualifying state construction projects. The EPD must demonstrate that the concrete achieves an environmental impact below limits set by the state for contracts exceeding $1 million and using more than 50 cubic yards of concrete, or Department of Transportation projects exceeding $3 million that include at least 200 cubic yards of concrete.